Mining consists of several complicated processes, and tailings is one that represents one of the most persistent environmental challenges in the mining industry. Tailings are left-over materials after the processing of mined ore. Apart from organic matter, they contain ground rock, unrecoverable and uneconomic metals, chemicals, and effluent from the process used to extract the desired products from the ore. According to research, mine tailings lead to the accumulation of heavy metals, acid rock drainage, dust emission, and surface runoff, with considerable effects on agricultural spaces, human health, and ecosystems.
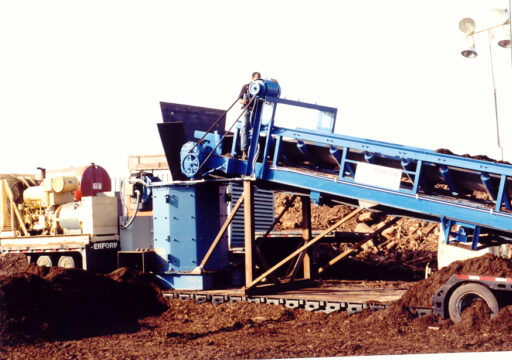
The reprocessing of tailings has long been a financial burden and a significant environmental challenge. Historically, these vast reservoirs of leftover material have posed contamination risks, from harmful chemical leaching to hazardous dust exposure, all while trapping valuable minerals. Environmental tech startup, Powermaster is turning this challenge into an opportunity. With a groundbreaking technology, they’re transforming the way mining companies reclaim and reprocess tailings, all while driving sustainability and profitability forward.
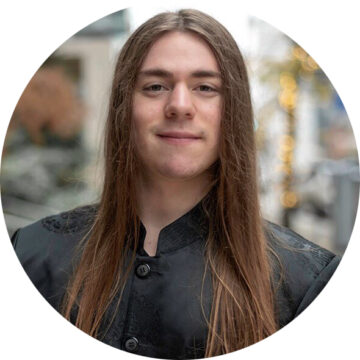
Tailings ponds and heaps have long been viewed as environmental time bombs—potentially leaching chemicals like arsenic and mercury into the surrounding environment. Powermaster’s technology dramatically reduces these risks by reclaiming tailings and transforming them into processed materials, which can be repurposed or safely disposed of
The Tech Panda spoke to Haiku York, CEO of Powermaster, who relates that they have pioneered a solution that not only addresses the pressing concerns of tailings but also enhances efficiency and mineral recovery in a way never seen before.
“The environmental benefits are clear. By reducing the volume of tailings and improving the recovery of minerals, we are lowering the risk of contamination. It’s not just about cleaning up—it’s about preventing future environmental damage,” says York.
“Tailings ponds and heaps have long been viewed as environmental time bombs—potentially leaching chemicals like arsenic and mercury into the surrounding environment. Powermaster’s technology dramatically reduces these risks by reclaiming tailings and transforming them into processed materials, which can be repurposed or safely disposed of,” he explains.
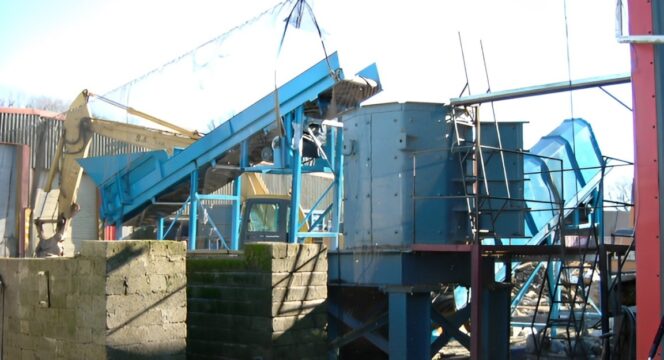
The startup is on a mission to lead the charge toward sustainable mining practices. The industry is increasingly under pressure to reduce its environmental footprint and improve resource efficiency. This technology offers a pathway to meet these demands, making it easier and more feasible for companies to transition to greener, more responsible operations.
Read more: {Startup watch: Global PCCS} Leveraging tech to help carmakers comply with ESG challenges
“Mining companies face a dual challenge: they need to be more efficient while addressing the environmental impacts of their operations. Powermaster’s technology enables them to do both,” York emphasizes. “This is the future of mining—smarter, cleaner, and more sustainable.”
The startup has achieved one tenth the energy usage as traditional comminution circuits, which means 90% less energy usage.
From 24 Inches to 45 Microns: A Game-Changing Leap in Processing
The revolutionary part about Powermaster’s technology is their ability to process materials from 24 inches down to 45 µm, all in one system. This unprecedented precision eliminates the need for multiple processing machines, dramatically streamlining operations and reducing capital costs for mining companies. The system can process material from 24 inches to micron sizes in one pass without the need for regrinding or screens.
By consolidating what used to require several stages of processing into one high-speed system, we’re not just making the process faster—we’re making it significantly more cost-effective. Mining companies can now reclaim and reprocess tailings with greater efficiency, using fewer resources
“This is a huge game changer,” says York. “By consolidating what used to require several stages of processing into one high-speed system, we’re not just making the process faster—we’re making it significantly more cost-effective. Mining companies can now reclaim and reprocess tailings with greater efficiency, using fewer resources.”
Unmatched Efficiency with Vertical Attrition Technology
At the core of Powermaster’s innovation is their high-speed vertical attrition system, capable of processing up to 400 tons of material per hour with micron-level precision. This revolutionary approach redefines how tailings are handled, allowing for more effective reprocessing and the recovery of previously unrecoverable minerals.
Our technology is designed to fundamentally change the economics of tailings reprocessing
“Our technology is designed to fundamentally change the economics of tailings reprocessing,” York adds. “By operating at such a high throughput with incredible precision, we not only reduce the amount of waste but also recover valuable materials that would otherwise be lost. It’s a win for the environment and for the bottom line of mining companies.”
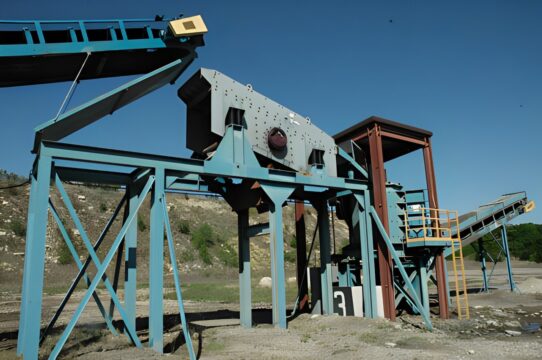
Powermaster’s system goes beyond simply managing waste. It maximizes the reclamation of valuable minerals from both intermediate and tailings materials, turning what was once considered an industry problem into a valuable resource. By using vertical attrition, the system grinds down material with incredible speed and accuracy, allowing the separation of fine particles while minimizing energy consumption and operational costs.
Partnering for Success
Apart from providing equipment, the startup is also forming partnerships. The team works closely with mining companies to tailor its systems to their specific needs and operational environments, whether it’s reprocessing tailings from precious metals, industrial minerals, or other sectors.
Read more: Continental’s Bengaluru plant is a smart & green factory for the auto tech industry
“With this technology, we’re not just selling equipment, we’re solving one of the industry’s most critical problems,” York concludes. “We’re proud to be at the forefront of this transformation and to be working with forward-thinking mining companies that want to make a positive impact both environmentally and economically.”
This innovation has the power to turn around even the most challenging mining operations. Where tailings used to represent an expensive problem, Powermaster now offers a sustainable and cost-effective solution. Mining companies that adopt this system can expect significant savings in terms of waste management costs, along with improved revenues from the recovery of previously untapped minerals.